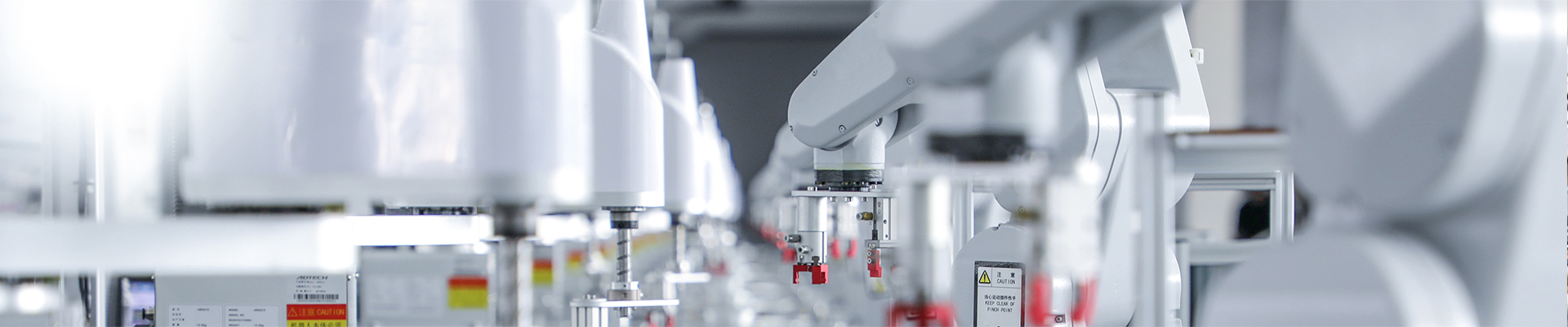
Grundlagen und vielfältige Anwendungsmöglichkeiten der Magnetkupplung
2025-03-24 08:31Magnetkupplung (Magnetische Wellenkupplung / Permanentmagnetisches Übertragungsgerät)
Eine Magnetkupplung, auch magnetische Wellenkupplung oder permanentmagnetische Übertragungseinrichtung genannt, besteht aus drei Kernkomponenten: einem Kupferrotor, einem Permanentmagnetrotor und einem Controller. Der Kupferrotor ist typischerweise mit der Motorwelle verbunden, während der Permanentmagnetrotor mit der Welle der angetriebenen Maschine verbunden ist. Ein entscheidendes Merkmal ist der Luftspalt zwischen den beiden Rotoren, der als flexible Verbindung fungiert und die Drehmoment- und Drehzahlanpassung zwischen Motor und angetriebener Maschine ermöglicht. Durch die Anpassung der Luftspaltgröße können Magnetkupplungen in Standard-, verzögerte, drehmomentbegrenzende und drehzahlregelnde Typen eingeteilt werden.
Gemäß GB/T 29026-2008 (Elektrotechnische Terminologie – Steuerung von Motoren) ist eine Magnetkupplung definiert als ein Gerät, das Drehmoment von einem Antrieb auf ein angetriebenes Gerät mittels magnetischer Kräfte überträgt. Man unterscheidet synchrone und asynchrone Kupplungen. Ihr Funktionsprinzip basiert auf Fortschritten in der Getriebetechnik, der Materialwissenschaft und den Fertigungsverfahren. Im 21. Jahrhundert, mit der Weiterentwicklung der Fertigungstechnologie, werden Magnetkupplungen nicht nur in konventionellen Maschinen eingesetzt, sondern ermöglichen auch den Betrieb von Geräten unter extremen Bedingungen. Die Permanentmagnet-Wirbelstrom-Übertragungstechnologie ist ein Beispiel für diesen Trend und bietet Energieeffizienz, Umweltfreundlichkeit und entspricht den Prinzipien der nachhaltigen Entwicklung.
Interne Struktur
Die Magnetkupplung besteht aus einer äußeren Magnetbaugruppe, einer inneren Magnetbaugruppe und einer Isolierhülse.
Sowohl die innere als auch die äußere Magnetanordnung bestehen aus radial magnetisierten Permanentmagneten mit abwechselnder Polarität, die kreisförmig auf kohlenstoffarmen Stahlringen angeordnet sind und eine Magnetkreisanordnung bilden.
Die Isolierhülse besteht aus nicht ferromagnetischen Materialien mit hohem Widerstand (z. B. austenitischem Edelstahl), um eine magnetische Isolierung zu gewährleisten.
Funktionsprinzip
Im Ruhezustand ist der Nordpol des äußeren Magneten mit dem Südpol des inneren Magneten ausgerichtet, wodurch kein Drehmoment entsteht. Dreht sich der äußere Magnet (angetrieben vom Motor), halten Reibung und Widerstand den inneren Magneten zunächst in seiner Position. Bei fortgesetzter Drehung entsteht jedoch ein Winkelversatz im Luftspalt. Dieser Versatz erzeugt eine Zugkraft auf den inneren Magneten und bewirkt, dass sich dessen Nordpol (oder Südpol) dreht. Diese berührungslose Drehmomentübertragung durch Magnetkräfte ist der Kernmechanismus magnetischer Kupplungen.
Hauptvorteile
1. Berührungslose Übertragung
Magnetkupplungen übertragen die Kraft durch magnetische Kopplung statt durch physischen Kontakt (z. B. Zahnräder oder Lager), wodurch mechanischer Verschleiß vermieden und die Lebensdauer erheblich verlängert wird.
2. Lärm- und Vibrationsreduzierung
Da kein physischer Kontakt besteht, ist der Betrieb nahezu geräuschlos und vibrationsfrei. Dadurch eignen sie sich ideal für geräuschempfindliche Umgebungen wie medizinische Geräte und Labore und verbessern gleichzeitig den Komfort und die Sicherheit am Arbeitsplatz.
3. Hohe Übertragungseffizienz
Magnetkupplungen minimieren Energieverlust und Reibung im Vergleich zu herkömmlichen mechanischen Kupplungen und steigern so die Effizienz. Sie werden häufig in industriellen Produktionslinien, Windkraftanlagen und anderen anspruchsvollen Anwendungen eingesetzt.
4. Leckageschutz
Ein zentrales Konstruktionsziel von Magnetkupplungen ist die Lösung von Leckageproblemen bei der Flüssigkeitsübertragung. Die Isolierhülse umschließt den Innenrotor und die angetriebenen Komponenten vollständig und wandelt dynamische Wellen-Körper-Dichtungen in statische Hülsen-Körper-Dichtungen um. Dadurch werden Leckagerisiken grundsätzlich eliminiert, was sie für Anwendungen mit hohen Dichtheitsanforderungen, wie beispielsweise in der Chemie- und Pharmaindustrie, unverzichtbar macht.